Developing highly functional materials to solve social issues with micro hole drilling technology - FiberCraze
2023/02/17
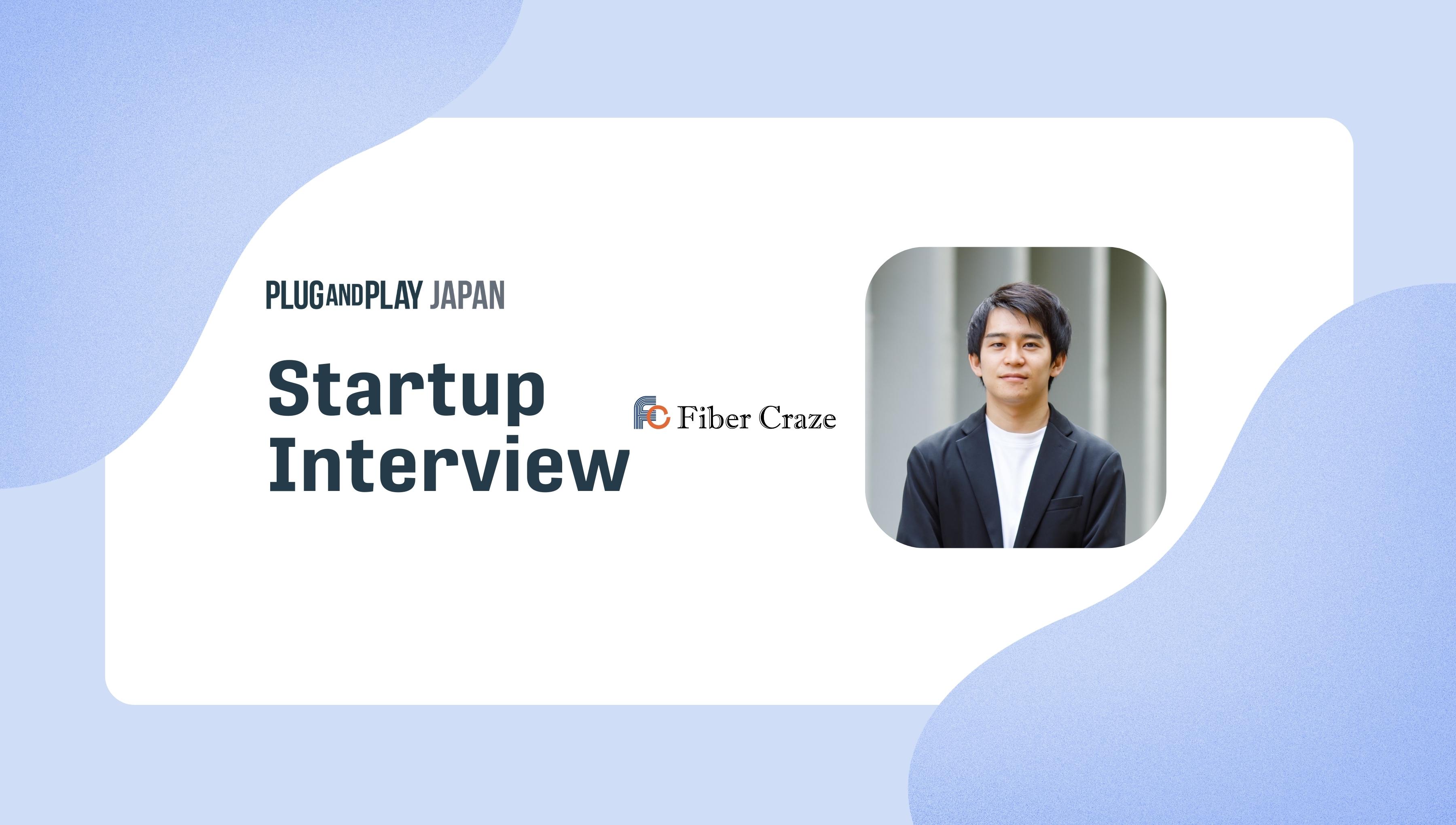
FiberCraze, is a startup from Gifu University whose mission is to “Solving social issues and contributing to people’s rich lives with the power of materials”. They participated in Plug and Play Japan’s New Materials Batch 3 program in 2022. We interviewed CEO Shunya Chosokabe, about the possibilities of materials technology as a Deeptech startup.
Entrepreneurial story of a startup from Gifu University
--Please introduce yourself.
My name is Shunya Chosokabe, CEO of FiberCraze Inc. The company was established in September 2021 as a student start-up. I am currently in the second year master’s program at Gifu University. Since last year, I took a leave of absence from school and have been fully committed to building my company. In terms of research, I belong to a laboratory that deals with polymeric materials and conducts research on the evaluation of physical properties, which is the core technology of FiberCraze.
(Image by FiberCraze)
--Please tell us about how you started your business.
When I started working in the lab, I saw great potential in our core technology. At the same time, I realized that despite the technology had been studied for more than 20 years, it was not yet available as a product in the market, so I wanted to implement it in society and promote it as a business, which was the trigger for commercialization and entrepreneurship.
--Can you elaborate on the core technology and your business?
Our main products are high molecular polymers and plastic-related materials. Among them, we specialize in the field of high-functional materials and develop not only fibers but also film materials. Our materials are called “porous materials” and can be used in films as membranes by taking advantage of their structure of nanometer-sized holes. For example, they can be used in membranes and filters that separate water from oil, or blocks viruses and bacteria and so on. In the case of fibers, the field of functional fibers is now attracting particular attention. For example, it is possible to add all kinds of functions to fibers and films through post-processing, such as insect repellency, moisture retention, deodorization, and antibacterial properties. We are developing highly functional materials using our proprietary technologies.
Perforation processing technology, which creates nano-sized holes in fibers.
--What are some of the trends in Japan and the rest of the world regarding the technology to confine ingredients in fibers?
Due to the coronavirus outbreak in recent years, antiviral functions are popular everywhere. In Japan, many fibers with antiviral, anti-odor, and antibacterial functions are becoming available. In addition, in order to prevent insect-borne diseases such as dengue fever and malaria, which are common in Southeast Asia and Africa, materials with insect-repellent functions for clothing are being actively developed, and a variety of new materials are emerging in the global market. There are mainly three processing methods used to add functionality to fabric. The first is coating technology, which is applied to the surface of the fiber material itself. The second is a kneading process in which the material is mixed with the necessary ingredients when the fiber is made. The third is a processing technology called microcapsule, which encapsulates the necessary ingredients and attaches them to the surface. The current trend is to use the above technologies to develop functional materials such as antibacterial, antiviral, and insect-repellent materials mentioned earlier. However, each processing method has its own issues, which is why we are here to solve those problems with our technology.
(Image by FiberCraze)
--Please tell us about your company's unique technology.
Our technology is called “perforation processing,” and an everyday example of its basic principle would be a phenomenon known as “stress-whitening.” When you bend a pencil board, the bent part of the board turns white. If you look closely at the bent area under a microscope, you can actually see a crack, which causes the area to look white. This phenomenon is the basis of our core technology and the beginning of our research, which led us to create nano-sized holes by exquisitely manipulating those cracks.
(Resource by FiberCraze)
--Can you explain the superiority and uniqueness of your technology?
There are three major advantages of our technology. The first is the ability to add abundant functionality through post-processing. When functional ingredients such as insecticide, antibacterial, and moisture-proofing are inserted into nano-sized holes, if they physically enter the holes, functionality can be added, which is a principle that sets us apart from existing technologies. The second is the component and its amount. According to experimental data from our lab, the amount of ingredients contained in the product is four times greater than that of existing coating technologies. Some components have been confirmed to contain up to 10 times as much if they are compatible with each other. Other advantages of our technology are the effectiveness and durability of the product depending on the material. Lastly, the ability to grant functions many times. If a component is trapped and then evaporates, it reverts back to its perforated state, so the function (component) can be re-imparted many times. As long as the material does not deteriorate, it can be reapplied and used again and again, which makes our technology so unique that no other technologies can offer.
--What is the mechanism or method of making nano-sized holes?
We use our proprietary machine to make the holes. The basic principle is as explained earlier: we drill nano-sized holes by applying force while slightly pulling the material in a manner similar to bending a pencil board. Since the conditions change depending on the material, there are various parameters such as the magnitude of the pulling force. We optimize these for each material and process the holes to be drilled. The drilled hole can also be opened or closed. In the case of opening, physically speaking, the hole is expanded by pulling the material. To close the holes, it is achieved by applying a special process as well.
(Image by FiberCraze)
--How do you encapsulate ingredients in a given material?
The material is first soaked in liquid extracted from an ingredient. It is the same principle as capillary action, which allows the ingredients to permeate the material. For instance, if you put a sponge in a liquid, it will quickly absorb the liquid, and the same principle applies to the holes. Once the material is fully soaked with the ingredient, we close the holes to complete the encapsulation.
--Is it possible to adjust the release of the encapsulated component? How does it work?
The release basically depends on the volatility of the component itself. For example, aroma and other fragrance ingredients are highly volatile and fly away quickly. On the other hand, if an ingredient is less volatile, it can be trapped for a longer period of time. Furthermore, by adjusting the degree of closure during the hole-closing process, it is possible to adjust the volatility of even highly volatile ingredients so that they are less likely to be released.
(Image by FiberCraze)
--Please tell me about the durability. Do the punched holes get bigger and bigger as they are washed and worn?
The encapsulated ingredient does not wear off just by washing the material since our nano-sized holes do not allow water to pass through. The holes do not reduce the strength of the fiber either. It can be used to weave fabrics and make clothes just like any other material. It is also unlikely that the holes will widen as it’s worn. If too much force is applied, it can stretch like most materials, but if not that much force is applied, there is no change.
Aiming to become a "materials infrastructure" for daily use.
--What product are you most focused on at the moment?
The fields we are particularly focusing on are the healthcare and agriculture industries. As for healthcare, we are developing products based on the concept of “wearable cosmetics.” In order to solve the problem of dry skin, we are working on ideas such as underwear and gloves that can moisturize the skin all day, in addition to applying liquid lotion or cosmetic cream. In addition, with many people suffering from skin irritation caused by non-woven masks due to the recent COVID-19 pandemic, we are also progressing with the development of masks utilizing fibers that are less prone to skin irritation. As for agriculture, we are making insect nets for leafy vegetable and fruit farmers, who are particularly vulnerable to pests. We are developing insecticide nets that have been specially processed and each thread has its own insecticide function, aiming to protect crops from pests. Since our technology has a very wide range of applications and competing products differ from one area to another, we believe it is very important to select the right partner that has a deep understanding of the industry and customers to which it will be applied. We would be happy to hear from any company that is interested in our services.
(Image by FiberCraze)
--Do you have plans to expand overseas?
First of all, we are thinking of expanding overseas, focusing on Southeast Asia and Africa. My initial motivation was to create effective solutions for dengue fever and malaria with insect-repellent clothing. I would like to proceed with the development so that we can expand into those regions as soon as possible. There are also needs for skin conditions and antiviruses that are common throughout the world, and we would like to work with appropriate overseas partners to expand our business there.
--What is your vision for the future?
From the very beginning, our vision has been to create a “material infrastructure,” a world in which our materials are incorporated into the clothes everyone wears and the materials everyone uses. GORE-TEX has been our benchmark, and we would like to contribute to solving industrial issues and play a supplementary role in enriching people’s lives with this material. Our current vision is to create a variety of functions in the field of high-functional materials that can be spread throughout the world as materials.
--What were your expectations before joining the Plug and Play Japan accelerator program?
The reason for my participation was that I wanted to verify the usefulness of the technology in fields other than our own project. Since I was biased toward the healthcare and agriculture fields, I thought this would be a good opportunity to verify a wide range of fields where the technology could be converted with 48 corporate partners. In addition to obtaining collaborative partners, I think the Plug and Play Japan program can also be used by deep tech startups to explore and expand their application fields.
--What were some highlights of the program?
The best part of the program was the opportunity to have discussions with companies in various fields and to brush up on our business strategies. I think this program was very good in the sense that we were able to consider a wide range of areas, not just our areas of expertise. In addition, we often work with companies on internal business strategies in the form of collaboration, joint development, and joint research, so we had two opportunities to brush up on how to conclude contracts and schemes for such projects. I was able to receive candid feedback from the experts and make use of some aspects immediately, so I think that was very good.
--Do you have a message for researchers, graduate students, or people in science who are considering starting a business?
As a researcher myself, I understand that there is a huge gap between academia and industry. From a researcher’s perspective, we tend to think in a technology-driven manner. However, if the product does not meet the needs, even if it is a good technology, it will not be utilized and will not be sought after, so it is important to visit customers and listen to their needs. We still have a ways to go, but we have been conscious of proposing solutions rather than selling technology. In fact, for our product for insect nets, we visited farmers many times and listened to what they said about the damage caused by insect pests. I think there are still only a few researchers who are also focusing on the industrial world aside from their studies. If you are even slightly interested in business, it is very valuable to be a part of that. If more people are willing to implement basic research in our society, Japan’s national power will definitely increase. I believe researchers possess the courage and persistence required to overcome the challenges of product development.